Angst + Pfister AG
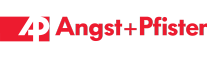
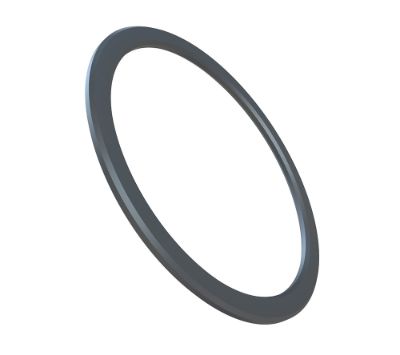
HITEC® DW EPDM
Explore product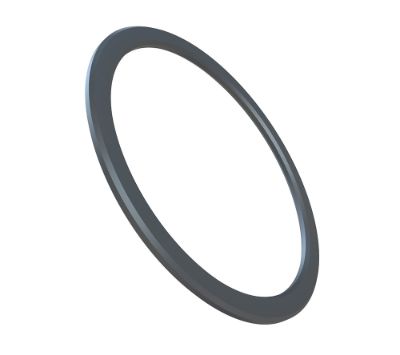
HITEC® DW EPDM
Explore product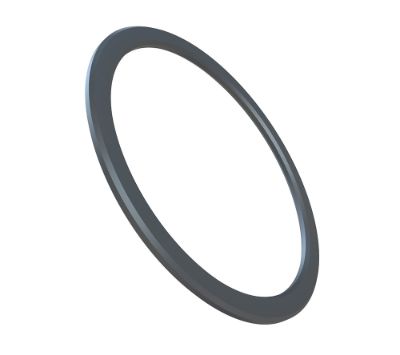
HITEC® DW EPDM
Explore productAddress
Angst + Pfister AG
Thurgauerstrasse 66
8050 Zürich
Switzerland
Discover more from us
About us
The Angst+Pfister Group, headquartered in Switzerland, has been a leading developer and manufacturer of technical components and engineering solutions for over a hundred years.
With local sales and technical support units as well as logistics centers worldwide, the company serves more than 20,000 customers in numerous industries in over 50 countries.
Angst+Pfister operates its own state-of-the-art research and development centers in Switzerland, Turkey and Italy, as well as its own production facilities for elastomer and rubber-metal parts and compounds in Switzerland, Turkey, Italy, Denmark, China and Vietnam. These are complemented by production partners in more than 15 countries, enabling Angst+Pfister to always be at the cutting edge of technology.
Angst+Pfister’s values are based on reliability and flexibility, as well as respectful and fair treatment of all people who have a relationship with us. As part of the proactive implementation of the UNGC principles, Angst+Pfister pursues the sustainability objective in all activities carried out to create a positive impact on our planet and society through pragmatic, reasonable and measurable initiatives.
Our product groups
Our application areas / Solutions
Downloads
Documents
Keywords
- Dichtungstechnik
- Trinkwasser
- Freigaben
- Kunststofftechnik
- Fluidtechnik
Our Products
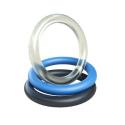
O-Rings / High-performance compounds
A comprehensive o-ring assortment
For more than 100 years, O-rings have been established as the preferred sealing elements in all branches of industry thanks to their simple geometry and high sealing performance. Angst+Pfister's range of O-rings covers the entire spectrum from high-performance elastomers to materials for standard applications – all at an excellent price-performance ratio. Additionally, Angst+Pfister also offers optimal sealing solutions for highly specific applications. Angst+Pfister is constantly expanding its product range and is thus successfully meeting the continuously increasing demands with regards to media and temperature resistance.
Our high-performance elastomers
With PERTEC® Angst+Pfister also offers an own range of high-performance elastomers featuring:
• Broad chemical resistance over a wide range of aggressive liquids
• Very good ozone-, weather-, age- and oxygen-resistance, also against mineral oils and greases
• Low gas permeability
• Temperature resistance from -60°C up to +200°C
• Almost all important approvals for the chemical, oil, gas, food and water industries
Here, compound production and a high reliability during the whole manufacturing process are crucial aspects. We offer state-of-the-art moulding, de-flashing, grinding, post curing and visual inspection processes in our in-house production.
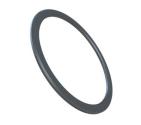
HITEC® DW EPDM
HITEC® DW EPDM
Complies with almost all drinking water regulations worldwide beyond February 2025 including KTW-BWGL
In order to be able to comply with the positive lists, many additives for the efficient production of seals may not be used or may only be used to a limited extent. Nevertheless, Angst+Pfister has succeeded in developing a drinking water compound that meets the requirements in the drinking water sector of and partially for the food and beverage sector, providing excellent mechanical properties as well.
Features
• Good mechanical properties within the wide temperature range of -57°C up to +150°C (short term in water and steam even higher)
• Suitable for the production of complex engineered moulded parts as well as for O-Rings
• For static and dynamic applications
• Crosslinking agent: peroxide
Benefits
• Black EPDM compound that complies with PAH Category 1
• Good mechanical properties
• Degradation resistant in contact with copper and brass
• Complies with almost all drinking water regulations worldwide beyond February 2025 including KTW-BWGL
• Possibility of surface treatment for lower friction according KTW-BWGL
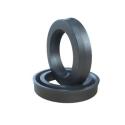
Molded seals
Special sealing applications require special solutions
Custom-fabricated molded seals (such as diaphragms, frame seals and housing seals or special elastomer lip seals) are called for in situations where specific application or operating conditions push standard sealing elements to their limits. These custom-molded seals are precisely tailored to the specific application at hand and, as their name implies, are manufactured using special forming molds and dies. Optimal shaping of the sealing lip and the right choice of material are crucial prerequisites for a reliably functioning molded seal.
Molded seals – the better solution for customer-specific applications
A molded seal specially designed for a specific deployment purpose offers substantial advantages over standard seals: Optimizing the shaping and selecting the right materials in order to fulfill all custom specifications guarantees maximum leak-tightness as well as an overall longer service life. Furthermore, the use of molded seals can simplify the construction of equipment components, which can largely compensate for the tooling costs required to manufacture these molded parts.
Advantages of using customized molded seals
• Optimum functionality because the seal geometry is adapted to fit the equipment or part design
• Good adaptability under low compression forces
• Minimal space requirements and simple groove design
• Easy and durable groove fixation by means of special retaining ribs
• Simple installation and easy handling
• Molded seals are superior to standard seals when it comes to bridging large installation tolerances, especially when plastic parts are involved
• Potential solution for large compression travel by means of specifically designed lip seals and advantageous force/displacement ratios (versus compact seals like O-rings)
• In dynamic deployment, optimization of sliding and static friction as well as breakaway torque through the shaping of the seal
• Use of specially designed lip seals for slow rotational or swiveling motion
• High-performance materials optimally suited for the customer-specific application
• Very good value proposition for medium and large series orders
With Angst+Pfister from task formulation to custom solution – we are there for you during the whole process:
1. We address the application problem together with you in an early development phase.
2. We design the seal environment together with you (receiving groove/seal contact area).
3. We design and execute the seal design, during which CAD-supported seal proposals can be discussed with you and FEM simulations of functionality can be conducted.
4. We produce the prototypes from pilot molds for the deployment tests (as well as lathe-cut molded seal prototypes where required in the case of rotationally symmetric geometries).
5. We receive your approval or we optimize the prototype and its seal geometry.
6. We produce the series mold and deliver first samples with an initial sample test report.
7. After approval of the series mold, we produce and deploy the series seal.
The perfect design and configuration of the geometry is the most important thing when it comes to molded seal. Getting the experience and creativity of the Angst+Pfister engineering team involved early on is the foundation for mutual project success. Contact us with your individual needs today!
A selection of molded seals, such as sterile seals and also molded parts, such as bellows, stoppers and cable sleeves can also be found on our online shop APSOparts!
Engineering – competence across the board
Angst+Pfister places its extensive experience in developing application-specific molded seals entirely at the service of its customers. Expert consulting services that range from choosing the right material to designing the seal geometry and defining possible surface treatments form the basis for our customized solutions. In addition to taking all application parameters into account, Angst+Pfister naturally also takes aspects such as cost effectiveness and easy assembly and installation into consideration. Alongside CAD (computer-aided design) services, FEM (finite element method) simulation is available during the development process to simulate especially challenging tasks. Angst+Pfister’s engineering expertise results in perfect molded seals that optimally meet customer-specific requirements and custom application specifications.
Fabrication – quality down to the tiniest detail
Perfect molded seals are the result of choosing the fabrication method best suited for the sealing application at hand. Injection, compression or transfer molding techniques are used depending on the geometry, unit production volume and material. Angst+Pfister has its own production workshops that are specialized in exactly these manufacturing processes.
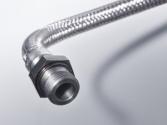
ASSIWELL® Metal hoses
ASSIWELL® hoses and fittings – the perfect connection
Within the APSOfluid® Fluid Handling Technology, Angst+Pfister offers a very comprehensive ASSIWELL® program with corrugated hoses, suitable fittings, corrugated hose lines and compensators made of stainless steel for almost all applications in various industries. Depending on the application, operating and installation conditions as well as the property of the fluids our specialists offer a tailor-made solution.
Corrugated hoses and their advantages
A hose line consists of the corrugated hose and the connection fittings as an interface to the customer's system connection. Corrugated hoses and folded spiral hoses belong to the metal hoses. The basic material for corrugated hoses are seamless or longitudinally welded, thin-walled tubes, into which corrugations are formed mechanically or hydraulically by special tools. The corrugation shape, wall thickness and corrugation spacing are responsible for the properties of the corrugated hose such as flexibility, bending behavior and pressure resistance. To increase the compressive strength, corrugated hoses are either double-walled or designed with single or double braiding. The hose braid serves to absorb the longitudinal force caused by the internal pressure (operating pressure). The braiding adapts flexibly to the state of movement (elongation) of the hose.
Our range of ASSIWELL® corrugated metal hoses
Our ASSIWELL® corrugated metal hoses are made of stainless steels such as 1.4404, 1.4541 and 1.4571, the braiding is made of 1.4301 or of the same material as the corrugated hose itself. The corrugated hoses can be used in a temperature range from -270°C to + 600°C. The operating pressure depends on the nominal diameter and geometries (wave form, number of braids and wall thickness) and is between 0.1 and 210 bar. Detailed technical information can be found on our data sheet ASSIWELL® Metal hoses.
Matching and high-quality standard fittings
We have high-quality standard fittings for corrugated hoses such as pipe sockets for cutting ring assembly according to DIN EN ISO 8434-1, nipples with external thread according to DIN EN 10226, flat sealing fittings with internal thread according to DIN EN 10226, 24° fittings with internal thread, external thread, welding neck flange and collar loose flange according to DIN EN 1092-1. For complete system solutions, the ASSIWELL® product range also includes special fittings, compensators, pipes and fittings according to customer specifications.
Our experience is an added value for you
Based on many years of experience in industries such as the electrical and mechanical engineering, steel industry, measurement and control technology, building technology, energy industry, railway industry, and automotive industry, Angst+Pfister provides its customers competently, flexibly and quickly already during the construction phase and optimizes the cables for individual installation situations. Just contact us with your individual needs!
Comprehensively certified
ASSIWELL® hose lines can be manufactured according to the following certificates:
• 97/23 / EG Pressure Equipment Directive (PED), Category I and II, Module A1 Swiss TS
• DIN EN 15085-2 railway applications – welding of rail vehicles and vehicle components, certification level CL1 Swiss TS
• DIN 3384 stainless steel gas hose lines according to DVGW and SVGW
• TPW / W 119-1 design and testing of corrugated hose connections for water installations up to PN 10 and temperatures up to +95°C according to SVGW
• TPW 119 design and testing of flexible connections for water installations according to SVGW