Pre-assembled modules improve efficiency, quality and sustainability.
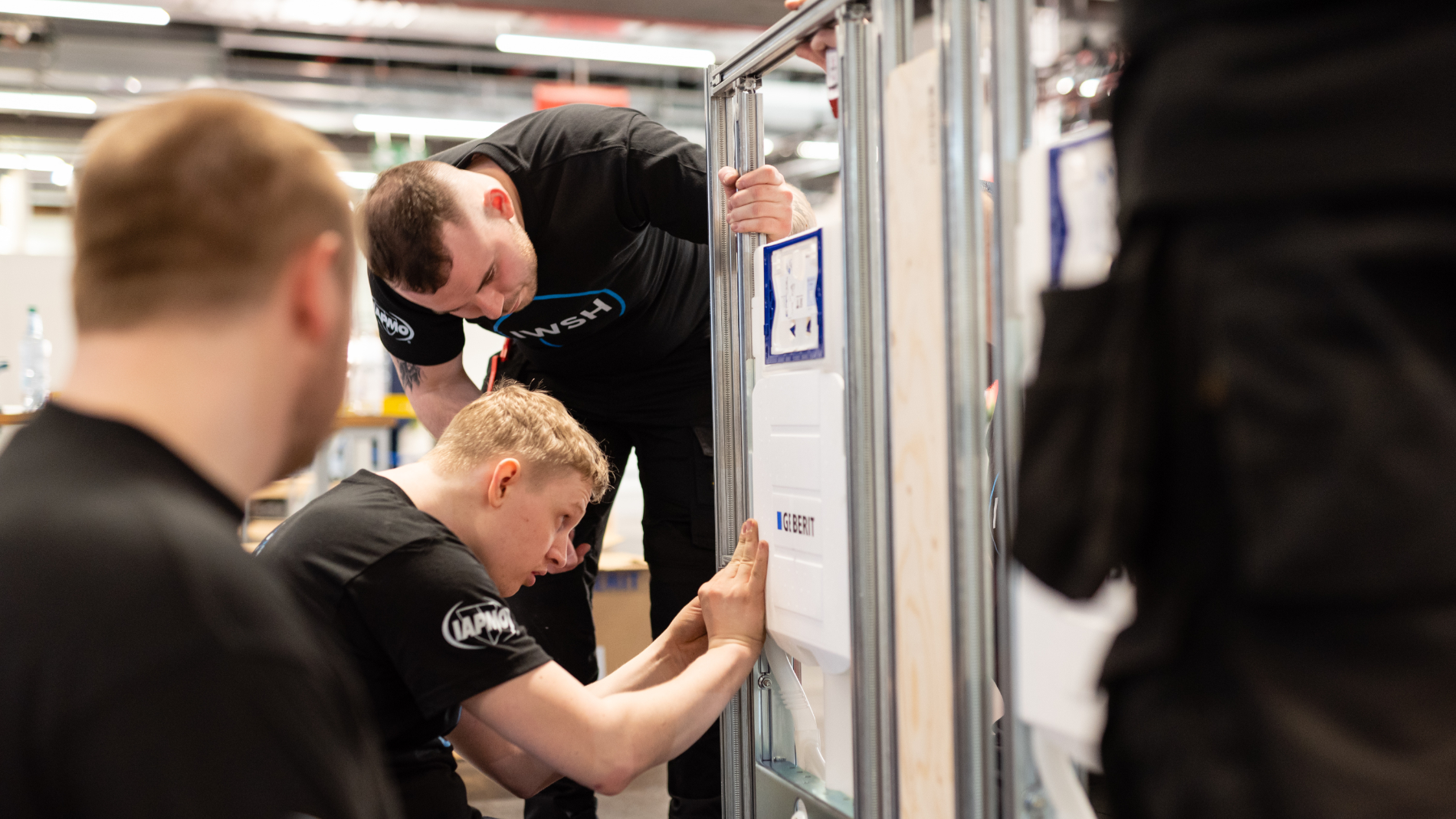
The increasing demands for efficiency, quality and sustainability in the building industry, coupled with the increasing lack of a suitably skilled workforce are leading to a greater need for industrial pre-assembly. This approach offers numerous advantages. Troubleshooting can be done in advance of installation on site, construction time can be greatly reduced, working time shifts from the building site to the workshop and the impact on the environment is minimised. Industrial pre-assembly can thus considerably reduce the workload for the trade.
Modern fabrication and assembly processes for building components
In industrial pre-assembly, building components such as pipework, plumbing fittings and heating components are produced in highly specialised manufacturing plants in advance of being transported to the building site. This procedure makes it possible to use state-of-the-art production processes including robots and CAD-controlled machinery, which ensure exact dimensions and conformity with current standards. This guarantees consistently high quality and precision engineered components.
As a result, elements fit together perfectly, which in turn makes for seamless installation on site. This is particularly advantageous for complex assemblies, which require a high degree of accuracy.
Time savings with industrial pre-assembly
A crucial advantage of industrial pre-assembly is the significant amount of time saved on site. The individual modules are prepared and tested centrally. Since many components are delivered fully assembled, the installation time is significantly reduced. As a result, working time moves from building site to the workshop or production hall, which in turn benefits the workforce: distances are shorter, there are no stairs to climb and there is no longer any need to carry heavy materials and components around. The savings in time are particularly significant for large-scale building projects, where tight schedules need to be observed.
Industrial pre-assembly is dependent on industrial logistics. Precise planning and organisation of transport corridors, as well as just-in-time delivery of pre-assembled components optimises the building process. This leads not only to faster completion, it also reduces costs, as downtime and delays are minimised.
Industrial pre-assembly in practice
Industrial pre-assembly is used in a number of different areas in the building industry. One obvious example is pre-assembly for installed bathrooms. Here, complete modules such as bathrooms and bathroom walls are prepared in production plants and then assembled on site. Modular construction enables rapid and efficient realisation of building projects such as hotels, where lots of identical bathrooms are required to be installed, one after the other, without any compromise on quality. And industrial process technology also pays off in the manufacture of heating system components, taps, mixers and fittings, as it guarantees large numbers of items with consistent quality and minimum costs. Ultimately, it is up to the individual companies in the sector whether they want the preparations to be completed in their own workshops or to request pre-assembled modules from the manufacturer.
Pre-assembly as a sustainable industry standard
Along with the obvious advantages with regard to efficiency and quality, industrial pre-assembly also contributes to sustainability targets. Because of the controlled conditions in workshops and manufacturing facilities, optimal use is made of materials and undue waste is avoided. At the same time, process-oriented solutions enable a more efficient use of resources, thus reducing the overall environmental footprint.
Visitors to ISH can learn about the latest innovations and technologies in industrial pre-assembly. This is where experts will be able to get first-hand experience of ways in which they can make their construction projects more efficient and sustainable by using modern production facilities and industrial production concepts.